Process Safety Gap Analysis
What is Gap Analysis?
Process Safety Gap Analysis is used to determine the following before the establishment of the Safety Management System (SMS) or Process Safety Management (PSM) in enterprises:
- Identifying the points where the current management system can feed the Safety Management System,
- Identification of missing points in terms of Safety Management,
- The connection between business culture and documentation,
- Systemic compliance determined by the level of competence,
- Cohesion of different levels within the organizational hierarchy.
. Gap Analysis is among the audit types and are used to determine the current level before a new system is installed.
A different point of view defines Gap Analysis as studies in which the difference between current performance and desired or potential performance is determined.
It is important that the system to be established is well-designed in advance, depending on the complexity, difficulty of adaptation and communication style between people/departments. They are usually carried out by independent and external persons.
Process Safety Gap Analyzes are usually performed on the same question lists as audits. Here, the required or desired level is to comply with the audit question lists and the differences between the current situation of the enterprise are determined.
ProSCon Process Safety Gap Analysis
ProSCon identifies compliance deficiencies of businesses with its Gap analyzes and supports the creation of the necessary roadmap to eliminate these nonconformities.
With the results of the analysis, answers to the following questions can be found:
- What is our compliance rate?
- What is our process safety level compared to competitors?
- Can we safely manage our risks?
- What should our roadmap be like?
ProSCon performs analysis at the level of the following elements in its Process Safety Gap Analysis:
- Leadership, Management and Employee Involvement
- Process Safety Information
- Process Hazard Analysis
- Change Management
- Operating Procedures
- Safe Working Practices
- Training and Safety Culture
- Mechanical Integrity
- Pre-Start-up Safety Review
- Emergency Management
- Incident Investigation
- Subcontractor Management
- Management System Evaluations
During the elimination of detected nonconformities, planning is made for each action in three different contexts:
- Working on it: Nonconformities that have started to be worked on
- QuickFix: Actions to produce fast solutions without disturbing the dynamism of the existing system
- Context Action: Actions that require conceptual change
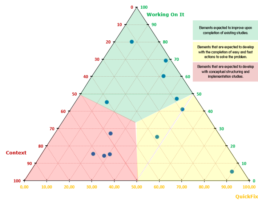
The scope of each non-conformance is important for establishing a process safety roadmap. While some elements are working in the system with a glitch, in some elements completely inoperative structures can be detected. In this way, it is decided in which elements the nonconformity will be eliminated without harming the business culture and habits with small touches, or in which elements it can work with radical changes and harmonize it with the business.
Effective and applicable recommendations are offered in the report for each of the detected nonconformities. This suggestion repository is also an input for the roadmap to be created.
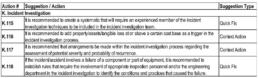
The action plans determined by the Process Safety Gap Analysis are evaluated together with the cultural change adaptation speed of the facility, and a process safety management (PSM) roadmap is formed.
Good and business-specific designed systems can be applied effectively when they are compatible with business dynamics and culture.
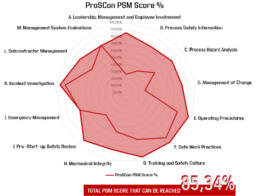
Our Services
Our Trainings

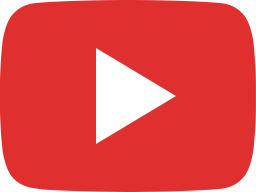
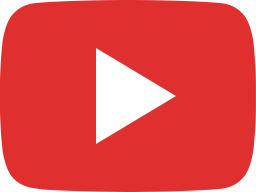
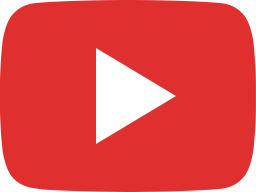
